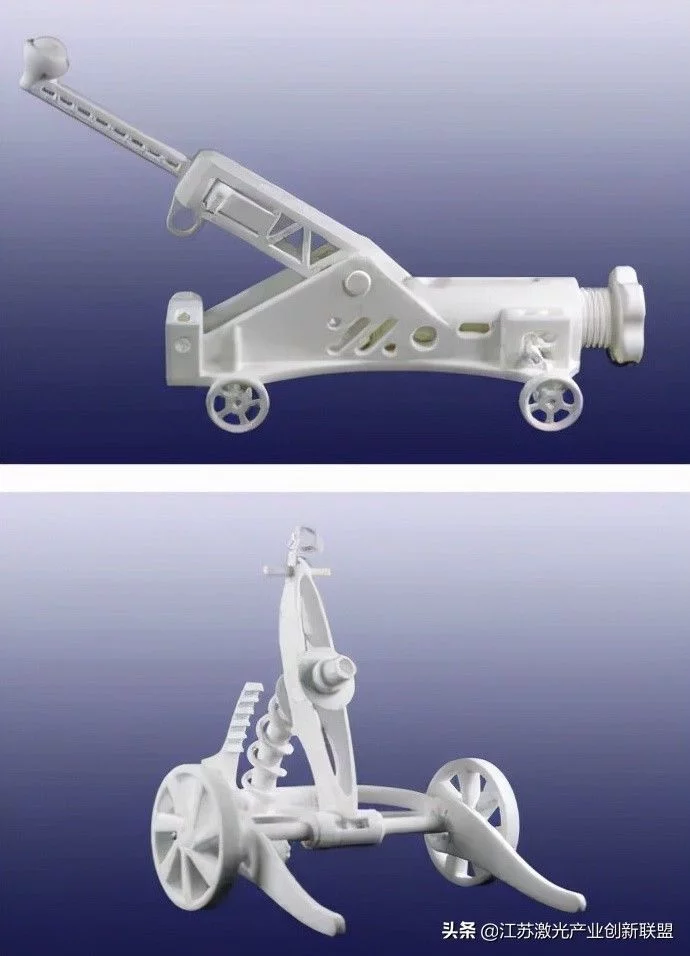
随着机器类型和可用材料种类的增加,原型的耐用性、强度、精度和尺寸都有所增加。因此,越来越多的原型被用来测试它们的功能,这被称为功能原型。成本仍然很高,除非原型在设计上很复杂,否则这种成本是不合理的。上图显示了一个由PA制成的弹射器的功能原型。来源:Courtesy of University of Paderborn.
1.介绍
在过去三十年中,随着3D打印和快速原型技术的发展,最近基于直接数字技术的增材制造(AM)在基于逐层整合的工程对应物制造方面引起了极大的关注,这与传统制造技术形成了对比。在几何复杂度、精度、制造速度和材料柔性等方面,AM可以与传统方法竞争,包括:;铸造和凝固、粉末冶金、金属成形和数控加工。根据ASTM F2792标准,AM被定义为材料逐层连接的方法,与减法制造技术相比,用于构建3D工程对应物。
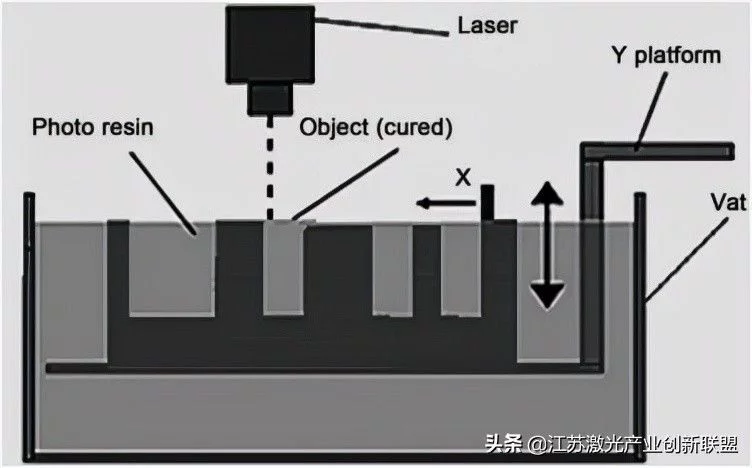
使用称为光激活聚合的过程选择性地固化液体光聚合物,以沿着切片3D模型生成的路径生成3D组件。液体光致聚合物在暴露于紫外线辐射时固化并变硬。该光通过电机控制的反射镜引导,并沿着CAD模型生成的路径移动,以选择性地固化树脂。在每个固体2D薄层固化后,在称为vat的光树脂浴中,将台或构建平台降低一层厚度。如图6.3所示,在已固化的前一层上添加另一层,直到施工过程完成,。
根据ISO/ASTM的分类,AM定义可以包括不同的类别,如:;还原型光聚合(VPP)、材料喷射(MJ)、材料挤出(ME)、粘合剂喷射(BJ)、薄板层压(SL)、粉末床熔融(PBF)和定向能沉积(DED)。在这七种AM技术中,VPP、MJ和ME是生产聚合物基结构的成熟技术。BJ可用于各种材料,但大多在陶瓷方面具有独特的潜力。与之相同,SL是所有类型材料的标准,其基于层之间的堆叠。然而,PBF和DED技术被很好地应用于3D金属复杂结构的制造。在提到的ISO/ASTM标准术语下引入了一些细分,而它们主要可以根据能源类型进行分类。
对于BDF,根据热源类型(如电弧、激光或电子束),可使用不同的术语选择性电弧熔化(SAM)、选择性激光熔化(SLM)和选择性电子束熔化(SEBM)。在DED的情况下,电弧增材制造(AAM)、激光增材制造(LAM)和电子束增材制造(EBAM)的相关术语是典型的。
金属AM技术中采用了多种金属和合金,以扩大3D零件生产中的AM工艺能力。AM零件还具有结构坚固性、内部缺陷、微观结构特征和机械性能等特征。在所用材料的背景下,考虑到钢、钛和镍基合金的广泛工业应用,文献的主要关注点是钢、钛和镍基合金。回顾文献中的AM报告表明,使用该技术可以获得广泛的微观结构特征和机械性能。LAM制造零件的最终质量在很大程度上取决于印刷材料的类别/等级以及采用的AM技术和加工参数。
在大多数情况下,观察到的微观结构特征与传统制造技术(如铸造、金属成型、粉末冶金或焊接和连接)截然不同。这些特征主要是由于材料逐层沉积期间的高度定向凝固机制和高冷却速率,导致各向异性特性。研究中观察到加工条件与微观结构特征之间存在良好的相关性,可以预测各种机械性能在压痕硬度、拉伸强度、断裂伸长率、磨损和疲劳抗力方面的不同趋势。
然而,AM在设计、复杂性和性能方面达到理想制造状态的关键问题之一(很少研究)可能是逐层处理期间的实时监控和实时控制。在这种方法中,通过在线测量沉积期间的峰值温度和实时冷却速率,并随后向系统发送反馈以进行调整,可以控制热动机械以实现所有层的均匀性。然后,通过关联凝固理论和可能的固态相变的冶金学,可以预测LAM沉积结构的微观结构特征和相应的机械性能。
Hu等人在基于激光的增材制造的传感、建模和控制方面进行了首次尝试。Bi等人后来试图表征和控制金属粉末在层层建造的金属结构表面上的沉积。Heralić等人通过一种新的迭代学习控制程序,证明了线馈LAM工艺期间沉积高度的控制。Bi等人、Muller等和Zhang等的后续报告研究了LAM工艺的其他工艺特征,以监测和控制生物适用材料中不同形状和成分的生产。Slotwinski等人在一项研究中测量并维持了孔隙率的形成和分布,以确定金属激光增材制造中沉积结构的可靠性。近年来,Shamsaei等人、Lee等人、Roehling等人、Vastola等人、Malekipour等人的几项研究报告了激光增材制造过程中的工艺参数优化、模拟建模、构建尺寸控制、基于光的高度控制和微观结构控制等研究。
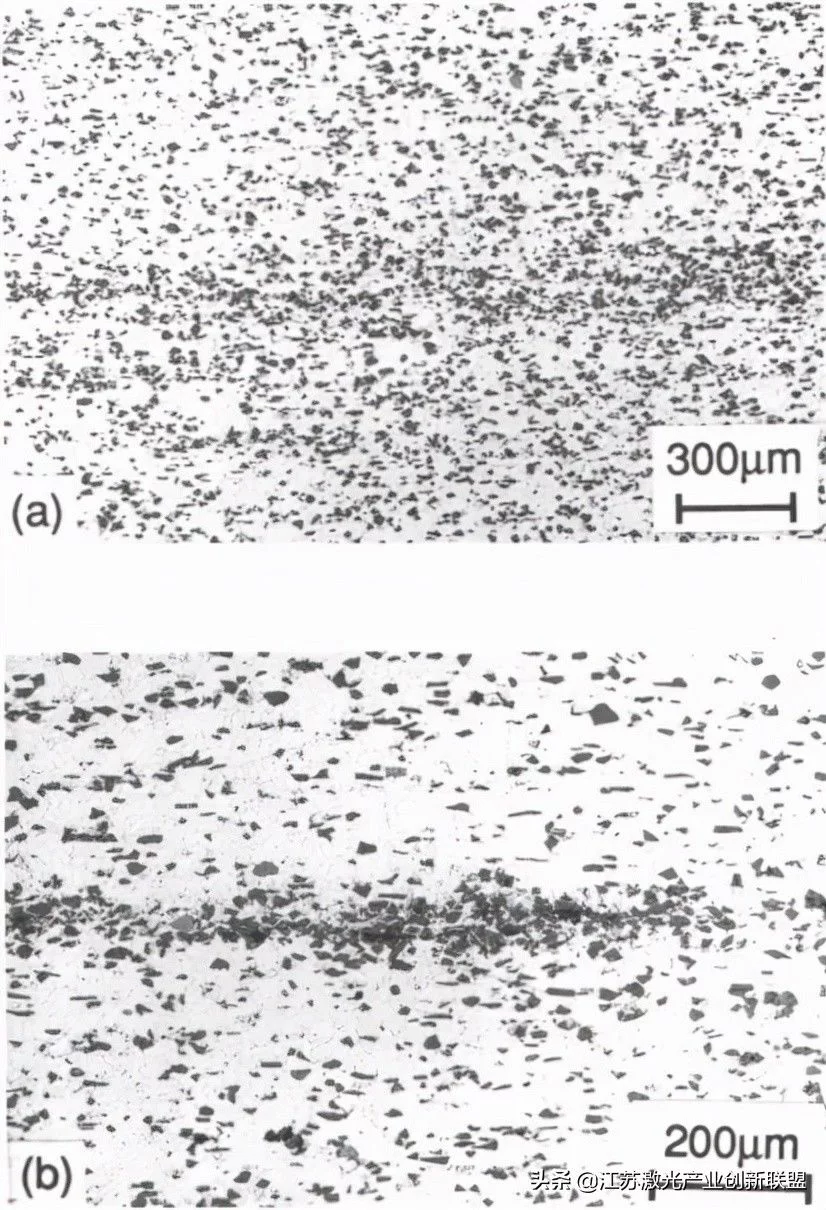
基于工业纯铝的颗粒复合材料挤压过程中富陶瓷带的形成(Shahani[1991])。(a)轻微带化,(b)更严重,带内出现空化。
尽管进行了大量的研究,但大多数研究集中在沉积的几何控制上,而在材料和机械性能控制方面的研究有限。在最近的一份报告中,Farshidianfar et al.介绍了一种方法,通过监测和控制冷却速率来监测和控制LAM过程中的微观结构变化。虽然使用该方法控制了多道沉积,但结果仅限于水平方向上彼此相邻且没有任何重叠的轨道沉积。然而,在LAM工艺过程中,各层在水平方向上彼此并排沉积,在垂直方向上彼此重叠,使用自下而上的方法形成最终的多层零件。
因此,本研究旨在实现一种新开发的闭环控制系统,作为先进的DED技术路线用于监测粉末馈送激光增材制造过程中金属镀层的微观结构和机械性能。在这方面,研究中考虑了S410-L级马氏体不锈钢,包括共析奥氏体到铁素体相变,以通过影响凝固行为研究实时冷却速度对最终微观结构的影响,以及影响逐层沉积期间机械性能的相关相变。对于开环沉积,考虑了三种不同的处理条件,无需任何监控(功率为800 W,移动速度为100、200和300 mm/min)以及闭环控制,以实现三种不同的恒定冷却速率(550、1100和1750°C/s)。然后,评估显微组织特征和压痕硬度,以确定这些特征与激光增材制造的关键工艺参数之间的相关性。
2.材料和方法
2.1.原材料
本研究以S410-L马氏体不锈钢为原料。所用不锈钢的化学成分包括0.14 wt%C、0.38 wt%Mn、11.51 wt%Cr和0.14 wt%Ni。该马氏体不锈钢材料由Alfa Aesar公司提供,为球形粉末,用于沉积层层结构。粉末的网目尺寸大于100,这意味着最大粒径小于150µm。此外,还提供了厚度约为6.35 mm的低碳钢基板,用于开始激光金属沉积。选择如此高的基底厚度只是为了减少沉积结构的变形,以制备良好的钢壁。基体变形与增材制造材料的最终微观结构之间没有相关性。然而,由于热沉效应,衬底的存在及其厚度会显著影响初级沉积层的晶粒结构。同时,在连续沉积累积层后,基板对产生的微观结构的影响可以忽略不计。
RP背后的思想是将3D CAD文件转换为二维截面,通过切片被设计/建造的对象的实体模型。为了启用切片过程,必须为3d模型生成一个三角文件(称为STL文件)。STL文件中的曲面是由三角形元素创建的网格。这个过程是通过软件自动完成的,stl格式是所有RP技术所接受的标准。根据对象的设计、定位和RP技术;增加支撑结构以支撑悬垂和避免在建造过程中下垂。根据所使用的技术,2D文件用于引导激光束(或沉积/切割头)“固化/固化”液体光聚合物树脂或沉积材料/切割片成等效的固体层。通过一层一层地建立一个三维对象的物理模型。立体光刻技术(SLA)在医疗领域应用的主要优势是,任何物体,无论其复杂性如何,包括自由形式的人体部位,都可以从其“CAD”文件中自动构建,而不需要工具或手动干涉。

快速原型的原则
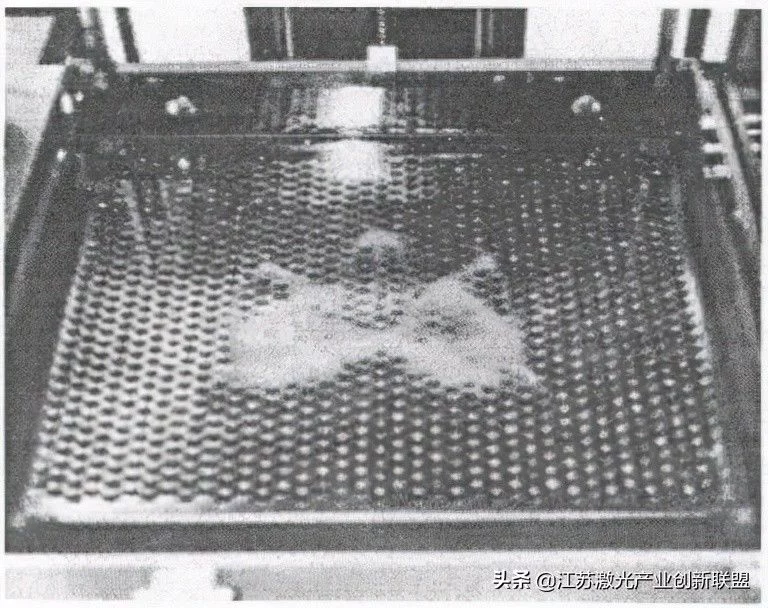
构建对象
此外,获得的精度可以非常高。使用立体光刻的缺点是,零件必须用一种特殊的医用级树脂制成,才能被带进手术室。即使使用医用级树脂,医用模型也只能作为手术过程中的参考,不能作为植入物使用(上图A)。展示了SLA机器的过程,该机器使用树脂来构建对象。这幅图展示的是建造头骨的示意图,其中各层被固化在另一层之上,形成头骨的“固体”。激光束从预处理(切片)的目标文件中接收每个切片/层的路径指令。层是建立底部向上,其中穿孔托盘是浸入一层,一次允许新的树脂层在上一层(上图B)在整个过程的最后,整个头骨将处于半固化的树脂状态。然后将底座托盘抬高,暴露对象和固化完成使用固化烤箱与紫外光。
2.2.闭环激光增材制造(CLAM)工艺
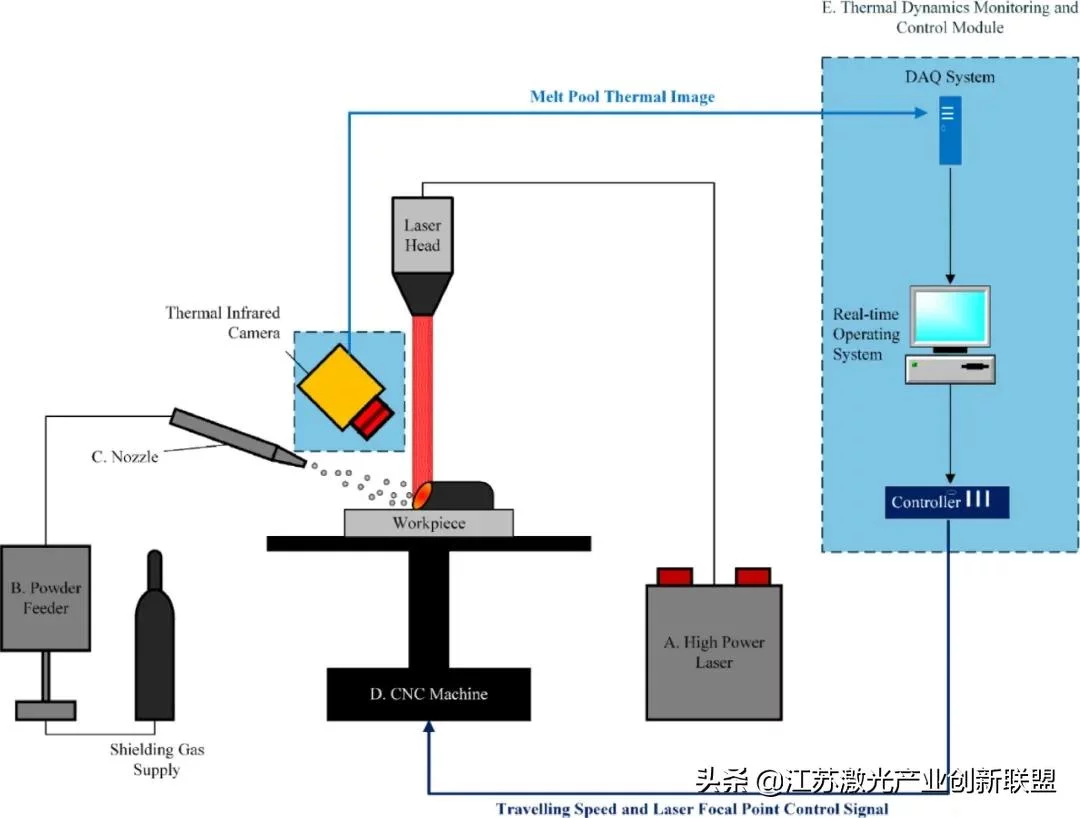
图1 闭环激光增材制造(CLAM)装置示意图。
为当前研究开发的闭环LAM装置示意图如图1所示。为了简化,整个闭环激光增材制造过程简称为CLAM。CLAM系统由五个主要部分组成:
(一)IPG公司采用YLR-1000-IC商业品牌制造的光纤激光器,功率更高,最大容量可达1.1 kW。该激光器在连续强度模式下工作,产生波长约1070 nm的激光束。
(二)粉末在激光诱导熔池内的喷射是使用粉末给料机进行的。因此,采用了SulzerMetco公司制造的商业代码为TWIN 10-C的进料系统,包括两个最大容量约为1.5窝的料斗。粉末的质量进给速度和作为保护气体的氩气流量通过该粉末进给系统进行控制。
(三)采用侧向喷嘴,通过保护气体的作用,将金属粉末送入基板表面。
(四)为了定位逐层沉积过程,实现了一台五轴自由度数控机床。对于这样一个所需的设备,由Fadal VMC 3016商业品牌制造的3轴CNC机床配备了两个额外的旋转轴,以提供动态运动。
(五)热动机械监控(TDMC)模块:基于红外视觉的监控系统实时捕获熔池热图像和历史。热红外摄像机(Jenoptik IR-TCM 384)记录沉积熔池和周围区域的实时热图像。使用NI LabVIEW在独立操作系统中处理这些记录的图像,以实时提取熔池的三个主要热动机械:(1)冷却速率,(2)熔池温度和(3)加热速率。数控行走速度由LabVIEW内部的操作系统控制,以实时将热动机械控制到一组特定的期望值。
LAM系统的工艺参数实时自适应调整,而不是在整个沉积过程中设置为恒定值。传统的工业LAM机器是开环的,不利用闭环反馈系统来控制熔池的几何形状或温度分布。在工业中,根据操作员和工程师的专业知识手动优化和固定工艺参数是很常见的。开发的CLAM系统提供了对该过程的深入了解,特别是在主要热动机械方面,以及在沉积过程中如何形成整体微观结构。因此,CLAM工艺提高了LAM产品的最终质量,并消除了典型工业应用中使用的时间密集型参数调整程序。
2.3.实施
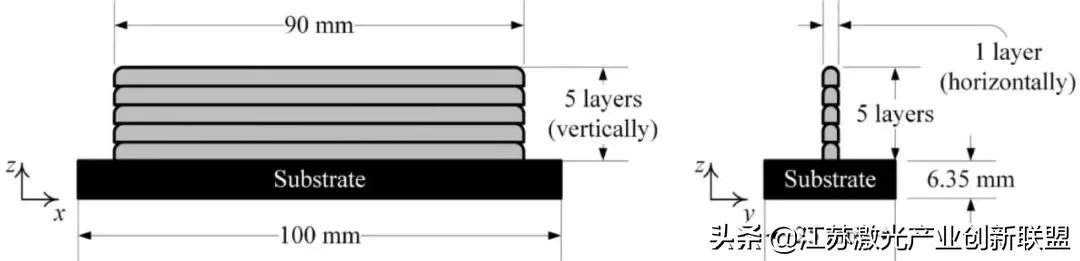
图2 多层LAM样本的示意图。
通过CLAM系统开发了一套多层薄壁结构,以研究闭环控制对LAM过程的影响。这些薄壁样品的示意图如图2所示。每个模型由五个相互叠加的垂直层(90 mm长)组成。表1列出了上述马氏体不锈钢薄壁的LAM试验条件。如上所述,三个参数用于LAM的开环沉积,三个参数用于闭环模式。对于开环和闭环条件,在所有实验中,激光功率始终设置为800 W。在开环沉积的情况下,激光横向速度在100至300 mm/min范围内变化,无任何控制。
表1 在800 W恒定激光功率下,S410-L马氏体不锈钢开环和闭环沉积的详细参数范围。
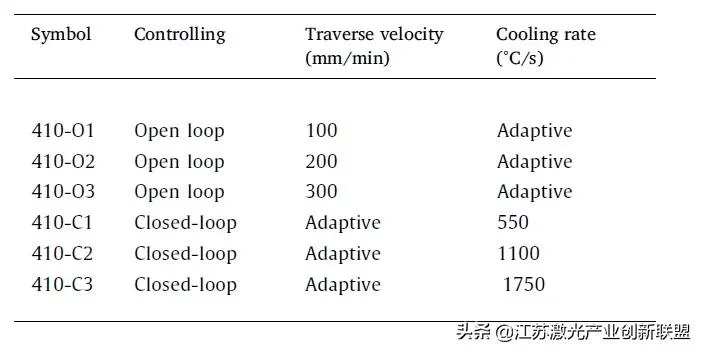
因此,根据加工过程中的应用热输入调整冷却速率。然而,在接下来的沉积过程中,通过实施闭环控制并使用TDMC模块,在800 W连续激光功率下,通过自适应改变移动速度,尝试将冷却速率保持在规定值550、1100和1750°C/s。然后,在表1(410-O1、410-O2、410-O3、410-C1、410-C2和410-C3)所示的六种加工条件下,沉积的马氏体不锈钢壁为五层相互堆叠的结构在以下章节中,考虑对厚度截面进行进一步的微观结构检查和机械试验。
2.4.微观结构细节
最初使用电火花加工(EDM)技术垂直于厚度平面对沉积壁进行横截面。实验中进行了标准的金相样品制备程序,包括在碳化硅金刚砂纸上进行机械研磨,然后在金刚石浆料上进行抛光。抛光后,为了揭示晶粒结构特征,使用化学成分为100 mL HCl-100 mL C2H5OH-5 gr CuCl2的“Kalling”化学试剂对S410-L马氏体不锈钢进行化学蚀刻,浸泡时间约为20 s。
采用光学显微镜(OM)和场发射扫描电子显微镜(FE-SEM)对晶粒结构进行了观察。使用奥林巴斯光学显微镜和JSM-6460 FE-SEM显微镜在低倍和高倍下完成这些检查。接下来,在含有胶体二氧化硅纳米颗粒的OPS溶液上再次抛光OM样品,以制备它们用于电子背散射衍射(EBSD)分析。为此,使用配备EBSD检测器的7600F JSMFE-SEM显微镜。
2.5.机械试验
在压痕显微硬度测试下,对机械研磨后和化学蚀刻前的最终抛光阶段所制备的LAM沉积物的厚度截面进行检查,以根据加工条件确定制造的层状结构的机械行为。硬度图和线轮廓测量均垂直于马氏体不锈钢LAM沉积壁的厚度截面进行。使用加拿大CLEMEX公司制造的微型压头绘图机进行硬度绘图。所有测量均在约200 gr的恒定正常负载下进行,保持时间约为15秒。对于映射和线轮廓测量,微压头位置之间的距离间隔控制为100µm。
3.结果和讨论
3.1.热历史
通过开环实验发展薄壁马氏体S410-L结构。沉积了一组由五层组成的开环样品,其热动力学如图3至图5所示。对于这些马氏体S410-L沉积,每一层沉积后组织的热动力学都发生了变化。然而,热变化似乎很小。结果表明,在相同的激光功率下,低速多层沉积体的熔池温度和冷却速率的变化比高速沉积体大得多。从图5可以看出,在高移动速度(300 mm/min)下,S410-L试样的熔池温度变化不大。相比之下,由于前一层的加热,其冷却速率急剧下降。
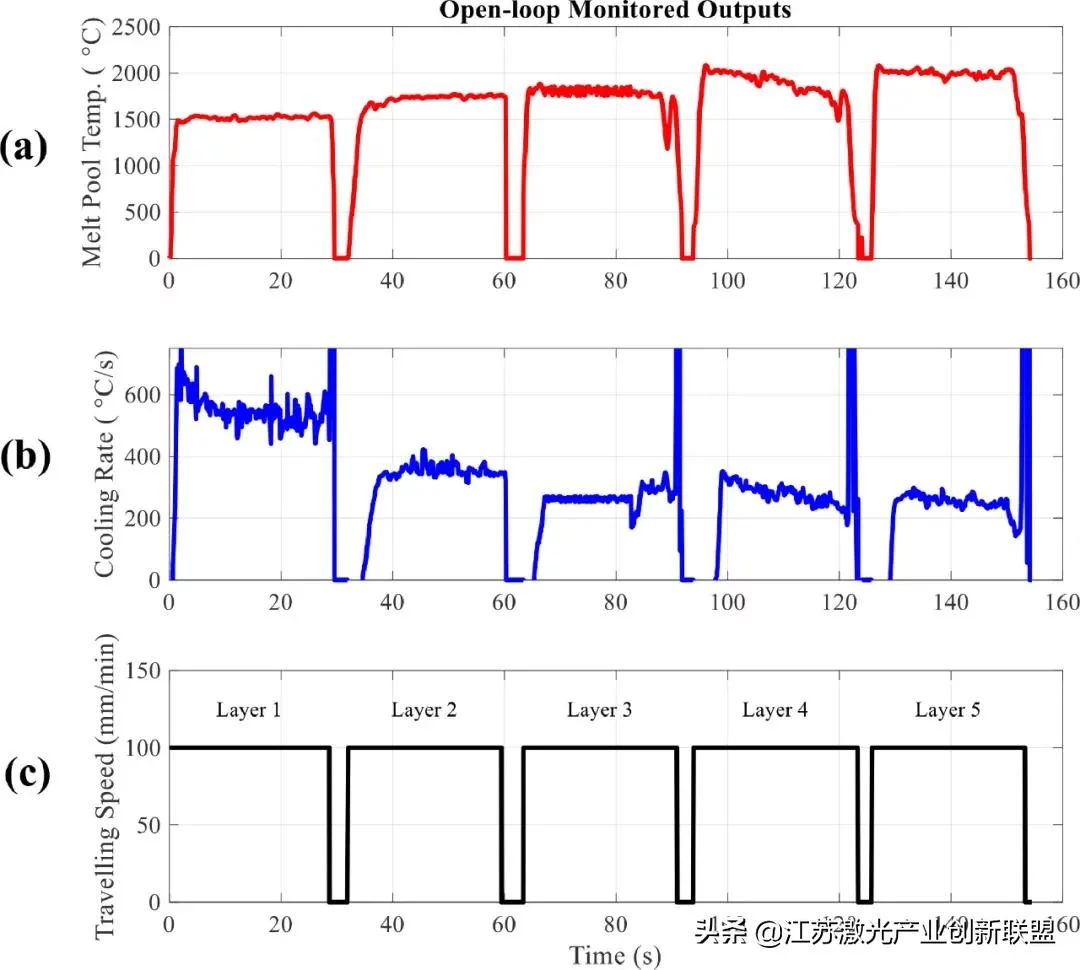
图3 样品410-O1的实时热动机械(移动速度固定在100 mm/min):在开环金属沉积下(a)熔体池温度,(b)冷却速率,和(c)恒定移动速度与处理时间的变化。
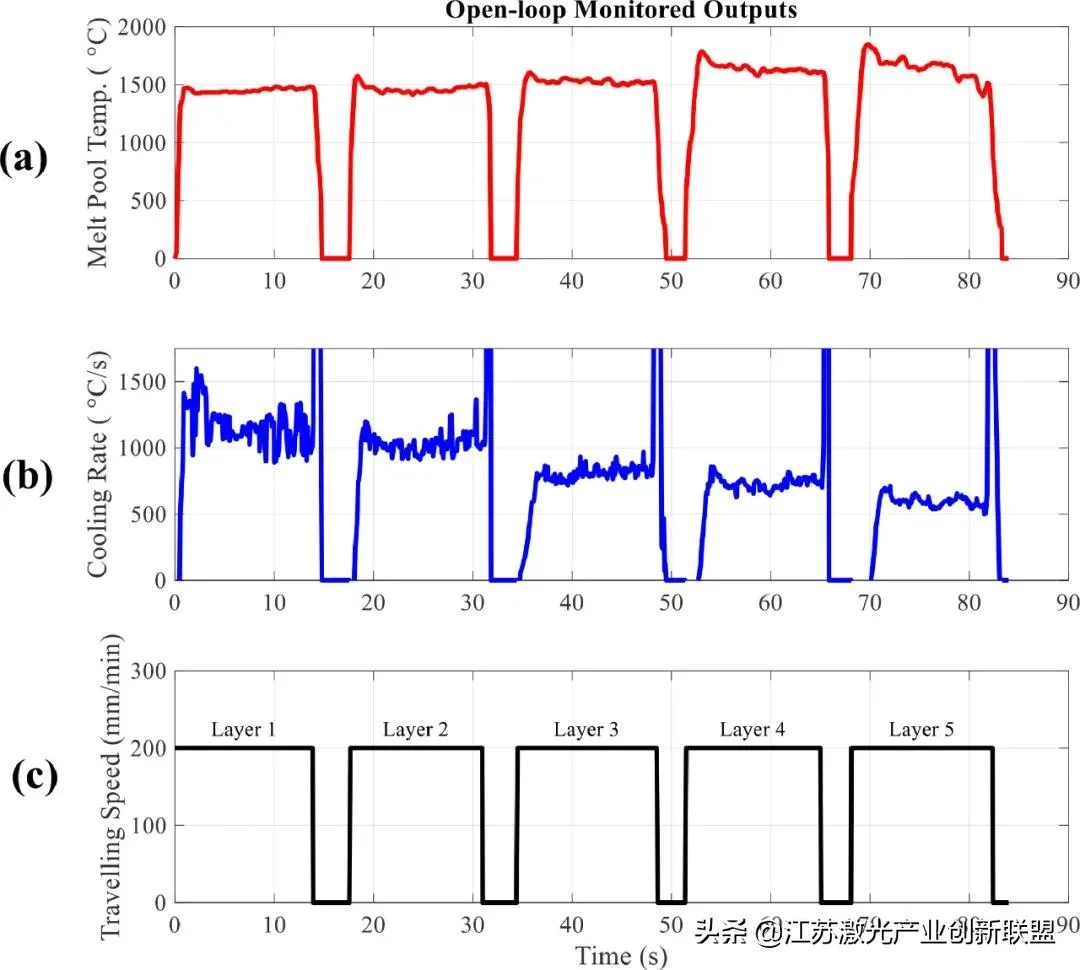
图4 样品410-O2实时热动机械(移动速度固定在200 mm/min):在开环金属沉积条件下(a)熔体池温度、(b)冷却速率和(c)恒定移动速度与处理时间的变化。
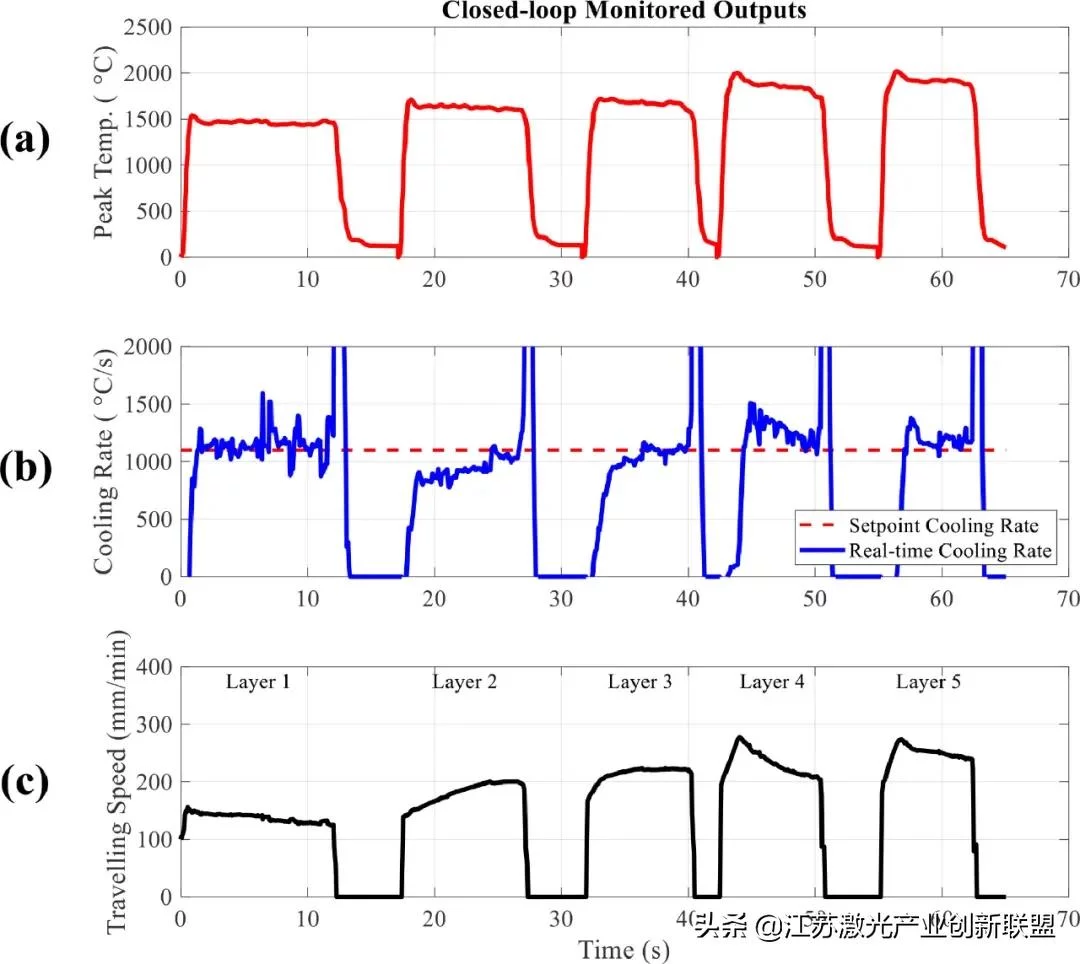
图5 样品410-O3实时热动机械(移动速度固定在300 mm/min):开环金属沉积下(a)熔体池温度、(b)冷却速率和(c)恒定移动速度与处理时间的变化。
因此,在不同的热动力学参数中,冷却速率在过程中变化的前景最为显著。当生产具有固定加工参数的多层零件时,可以观察到热动力学的显著变化。然而,这些变化的幅度取决于工艺条件,如加工参数、材料和区域几何形状。由于LAM是一种自底向上的制造方法,这些变化可能会导致最终结构中的微结构和机械性能不均匀)。
尽管CLAM过程的总体结果令人鼓舞,但在某些层的开始部分存在超调,这可以通过改进控制器和参数调整过程来解决。每层末端的冷却速率也存在超调,这是LAM工艺本身的一个特征,可忽略为每层沉积层末端突然激光关闭导致的特征,对最终微观结构没有任何重大意义或影响。
从马氏体S410-L材料中产生了一组薄壁沉积。闭环样品也使用三种受控冷却速率生产:500℃/s、1100℃/s和1750℃/s。闭环S410-L样品的实时热动机械如图6、图7、图8所示。如前所述,通过调整移动速度,将这些样品中的冷却速率控制在所需的设定值。当闭环样品的熔池温度发生变化时,通过提高沉积过程中的移动速度来精确控制其冷却速率。比较这些结果表明,监测和控制S410-L样品中的冷却速率需要移动速度的微小变化。
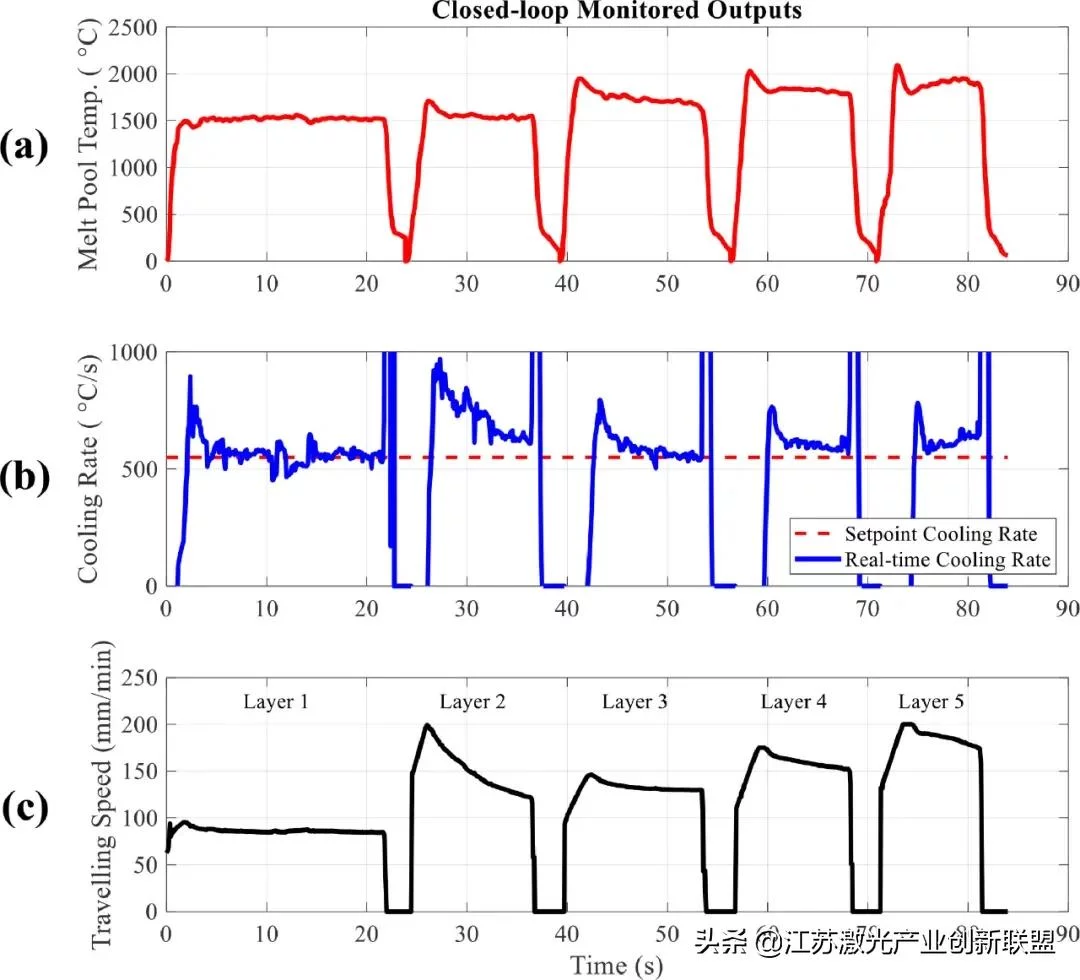
图6 样品410-C1实时热动机械(冷却速率控制在550°C/s):(a)熔体池温度,(b)冷却速率,(C)和移动速度采用与处理时间。
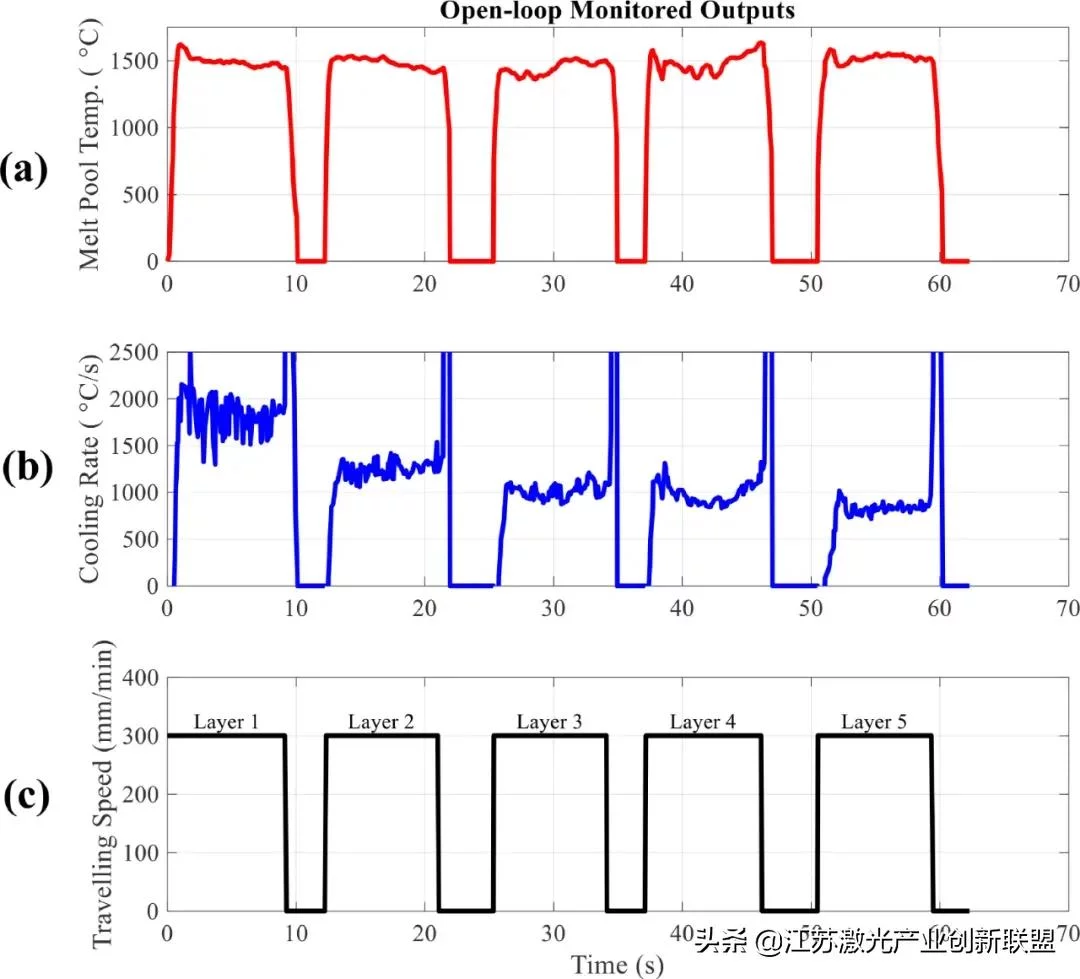
图7 样品410-C2实时热动机械(冷却速率控制在1100°C/s):(a)熔体池温度,(b)冷却速率,(C)和移动速度采用与处理时间。
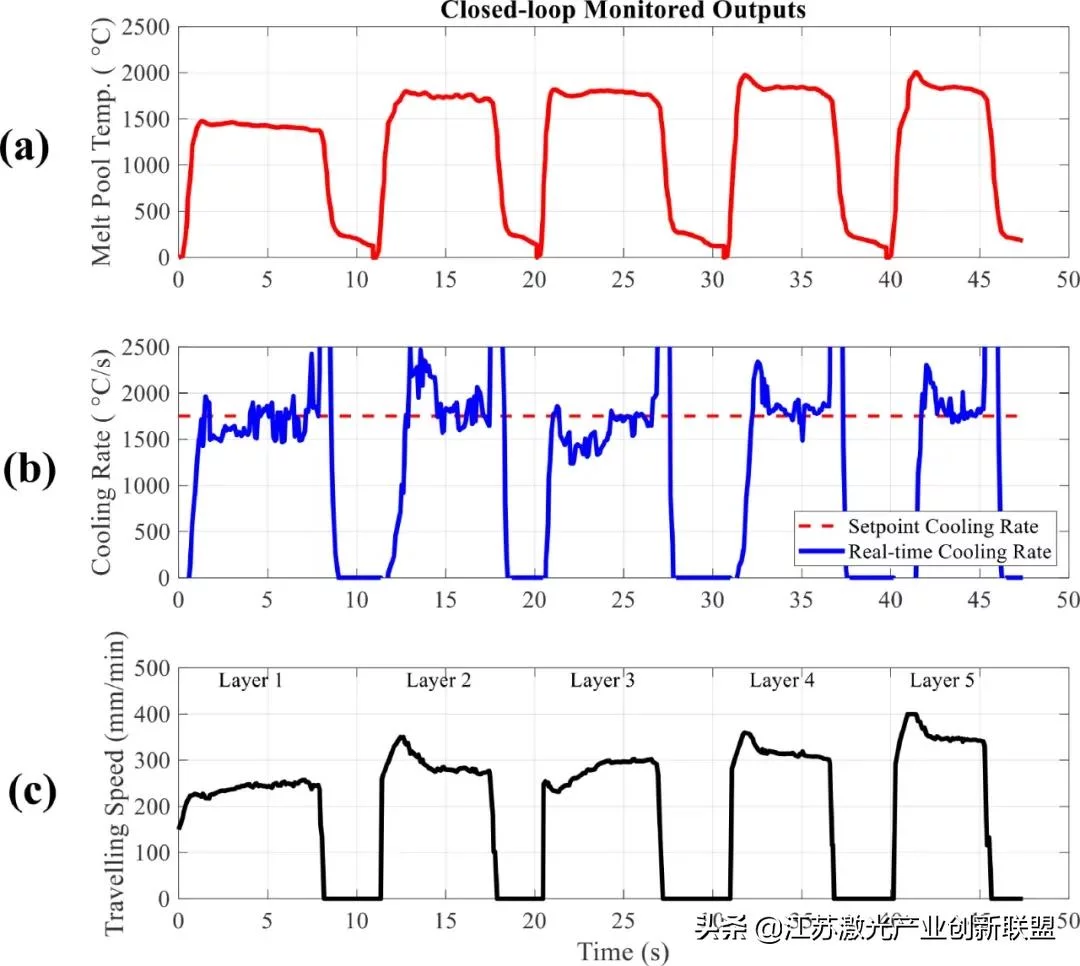
图8 样品410-C2实时热动机械(冷却速率控制在1750°C/s):(a)熔体池温度,(b)冷却速率,(C)和移动速度采用与处理时间。
此外,如图3、图4和图5所示,与开环沉积相比,在所有加工条件下,这些闭环沉积的熔池峰值温度和冷却速率的波动程度较低。此外,值得注意的是,图3、图4、图5、图6、图7、图8中的漏峰冷却速率不是真实的,因为这些点对应于激光加热的停止点。事实上,每层沉积过程中通过温度-时间冷却循环的实际冷却速率是高原区域波动趋势的平均值。因此,尽管遗漏了虚假的最大值,但这些数字集中于更清晰地说明所提到的真实热区。当与图6中的冷却速率分布进行比较时,图6中的冷却速率的波动程度与7和8相比是突出的。其原因在于,通过将冷却速度提高到所需的更高的比值,激光材料加工的物理稳定性会降低。事实上,更快的处理会导致监控步骤出现更多的振荡。
3.2.显微结构表征
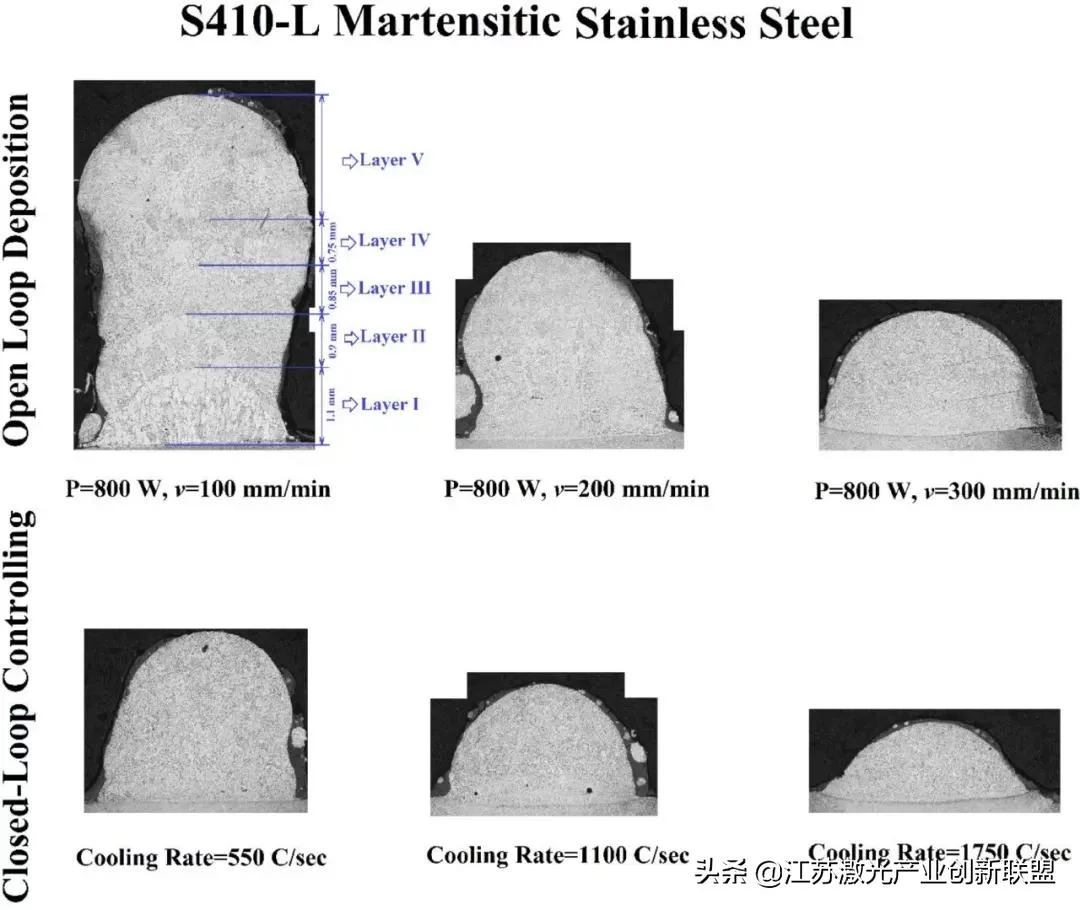
图9 开环和闭环样品S410-L的宏图。
图9中报告了开环和闭环S410-L马氏体不锈钢沉积的宏观结构剖面。在此,由于固态中发生马氏体相变,微观结构发展与凝固后完全不同。在其他加工条件下比较这些结果,很难区分马氏体不锈钢沉积层之间的边界。这也可归因于发生马氏体相变,而不是LAM工艺快速冷却引起的奥氏体-铁素体相变。
此外,可以发现,在所有工艺条件下,所有S410-L LAM沉积的微观结构均为完全马氏体。对于具有较高热输入的开环样品(样品410-O1和410-O2),可以观察到范围广泛的马氏体板条尺寸和形态。另一方面,随着冷却速率的增加,所有样品的微观结构变得更加均匀,而LAM样品的高度则降低。如图9所示,闭环S410-L样品的宏观结构比开环样品均匀得多,开环样品在所有处理条件下都可以突出显示。这归因于在闭环沉积下而不是开环沉积下的逐层制造过程中更均匀的冷却速率,这导致固态发生马氏体相变的更均匀性以及随后马氏体板条的诱导尺寸分布。
在图10和图11中分别显示的开环和闭环S410-L马氏体沉积的显微图中也可以观察到类似的结果。图12和图13分别给出了开环和闭环马氏体不锈钢镀层微观组织的高倍FE-SEM图像,并进行了对比。在不同的加工条件下,各层的显微组织均为马氏体。最突出的问题是开环试样层中马氏体板条尺寸和形貌的变化。

图10 开环S410-L样品显微图。
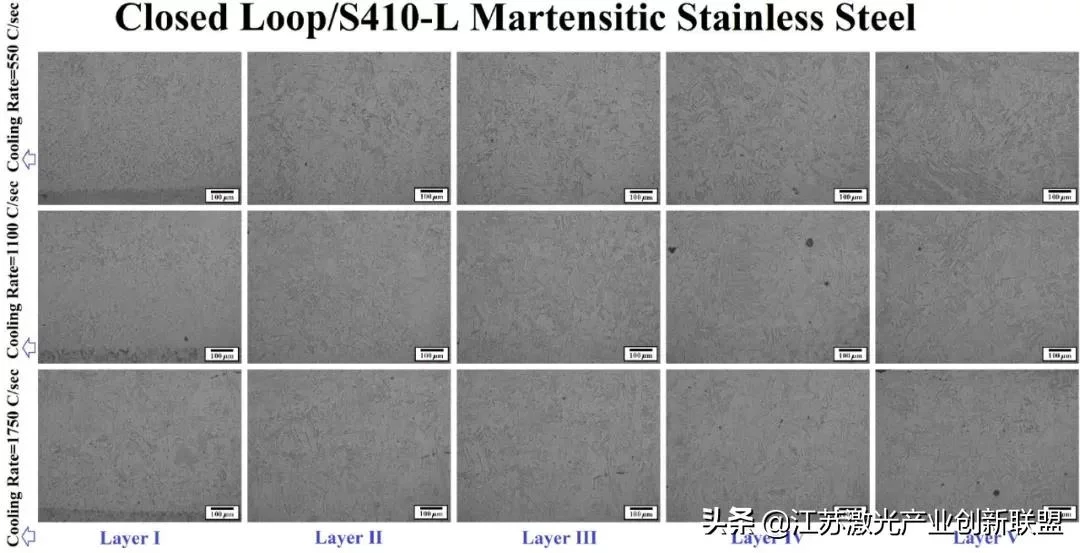
图11 闭环S410-L样品显微图。
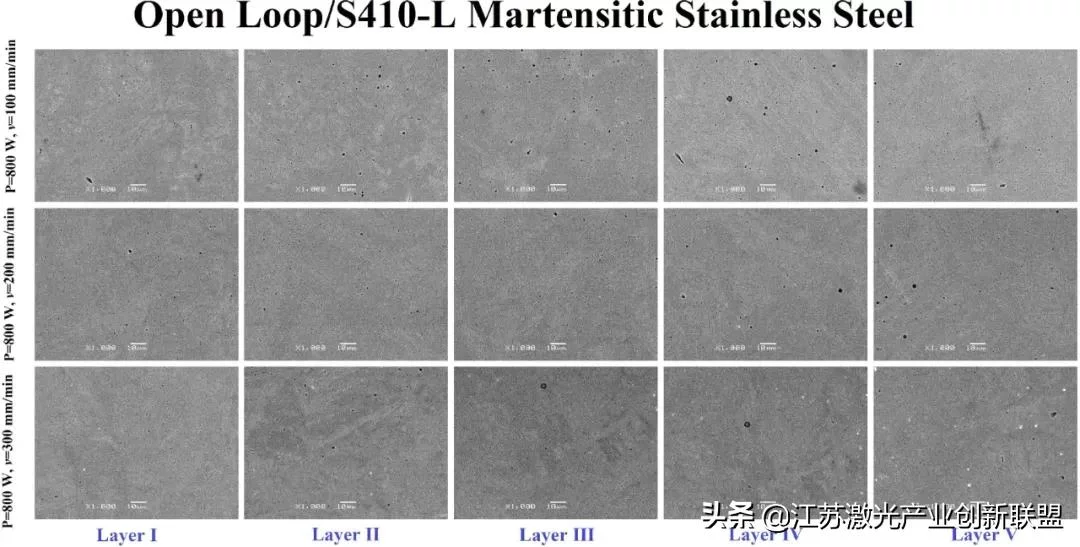
图12 开环S410-L样品的FE-SEM图像。
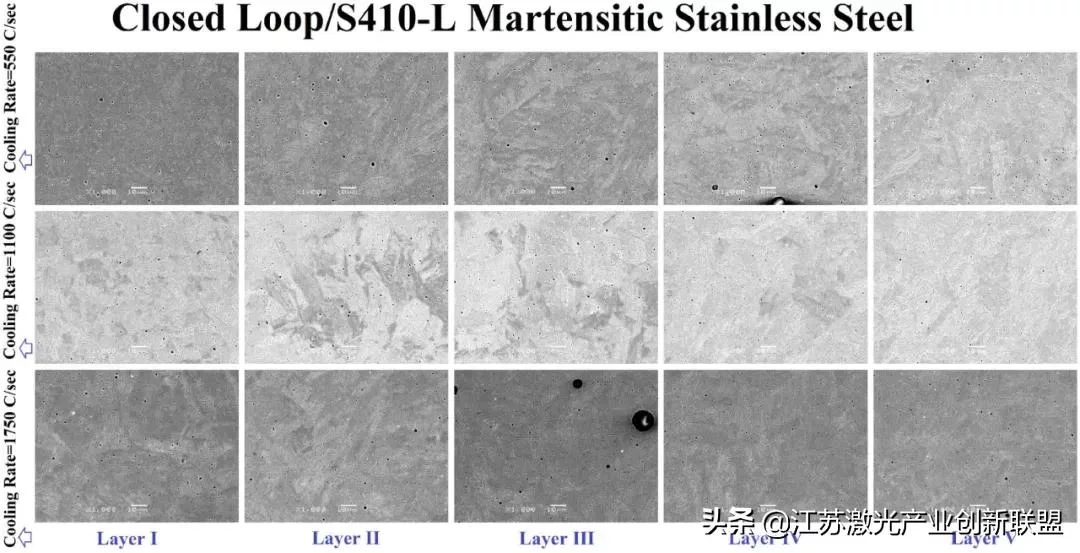
图13 S410-L闭环样品的FE-SEM图像。
冷却速率的变化引起层间的变化,如图3、图4、图5所示的开环沉积。闭环S410-L样品层之间的微观结构非均质性比开放样品层要低得多(见图11和图13),这是由于闭环沉积的动态热结果波动较小(见图6、图7和图8)。在S410钢马氏体相变的发生上,主动冷却凝固后奥氏体向铁素体相变可以协助代micro-twins沿着边界根据shear-based变形机制,它可以区分马氏体板条之间的边界。
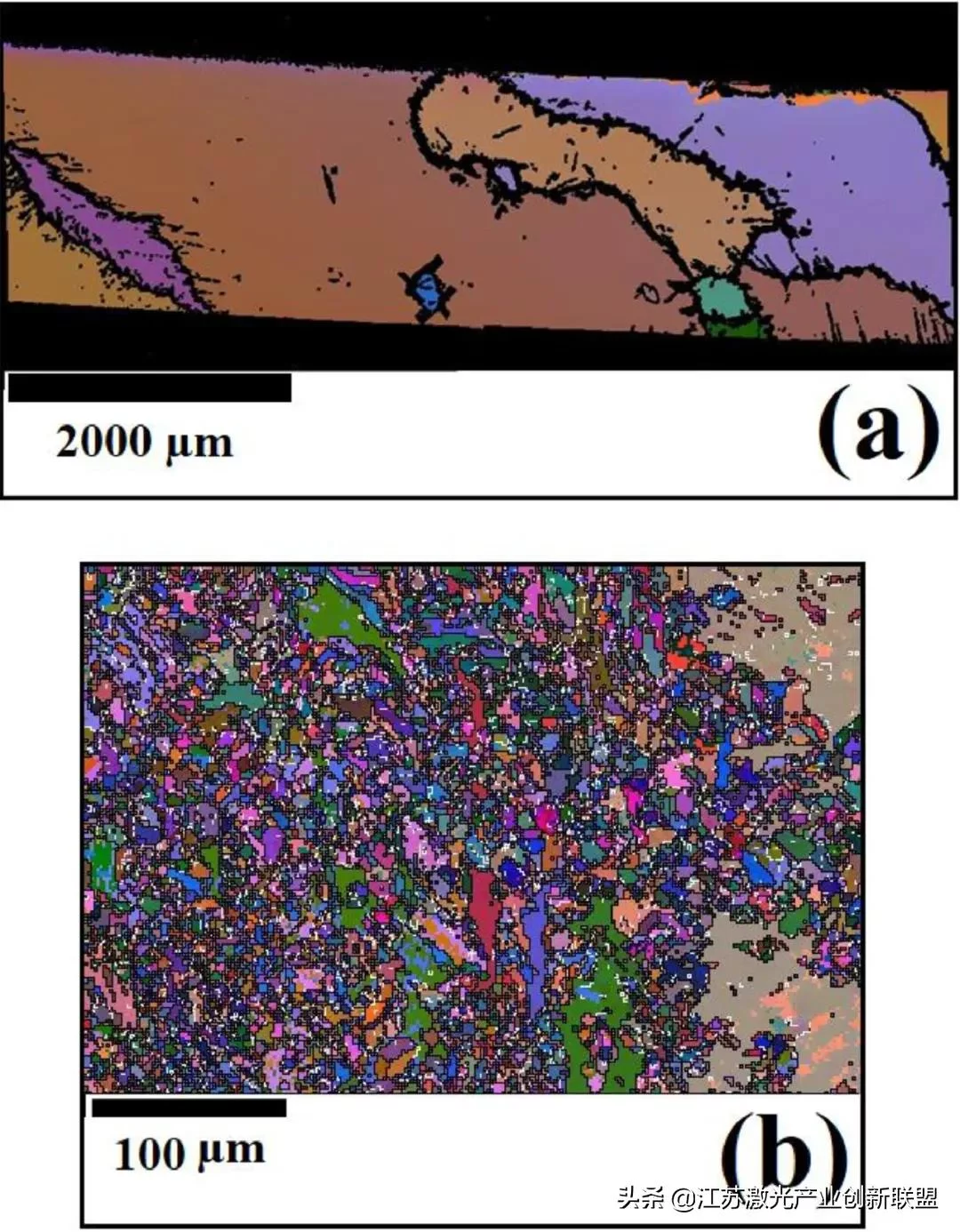
图14 EBSD图显示了(a) 410-O1和(b) 410-C1层的第一沉积层的晶粒结构。
在图14中,如EBSD分析所示,在开环和闭环条件下,从沉积的第一层马氏体不锈钢壁上显示了由此产生的晶粒结构图。马氏体相变过程中微观孪生机制的运行可以显示为马氏体板条之间的锯齿线。随着冷却速度的增加,马氏体板条的尺寸细化,随着体积分数的增加,这些微孪晶的畴变细,分布更加均匀。基于上述EBSD分析,微孪晶是控制S410-L钢在激光增材制造的逐层沉积过程中马氏体相变的一种非常常见的机制。
3.3. 机械性能
基于压痕维氏显微硬度响应,根据测量剖面和各层之间的图,评估了LAM沉积马氏体不锈钢结构的机械行为。分别在开环和闭环条件下沉积的马氏体样品410-O1和410-C1的硬度图如图15所示。
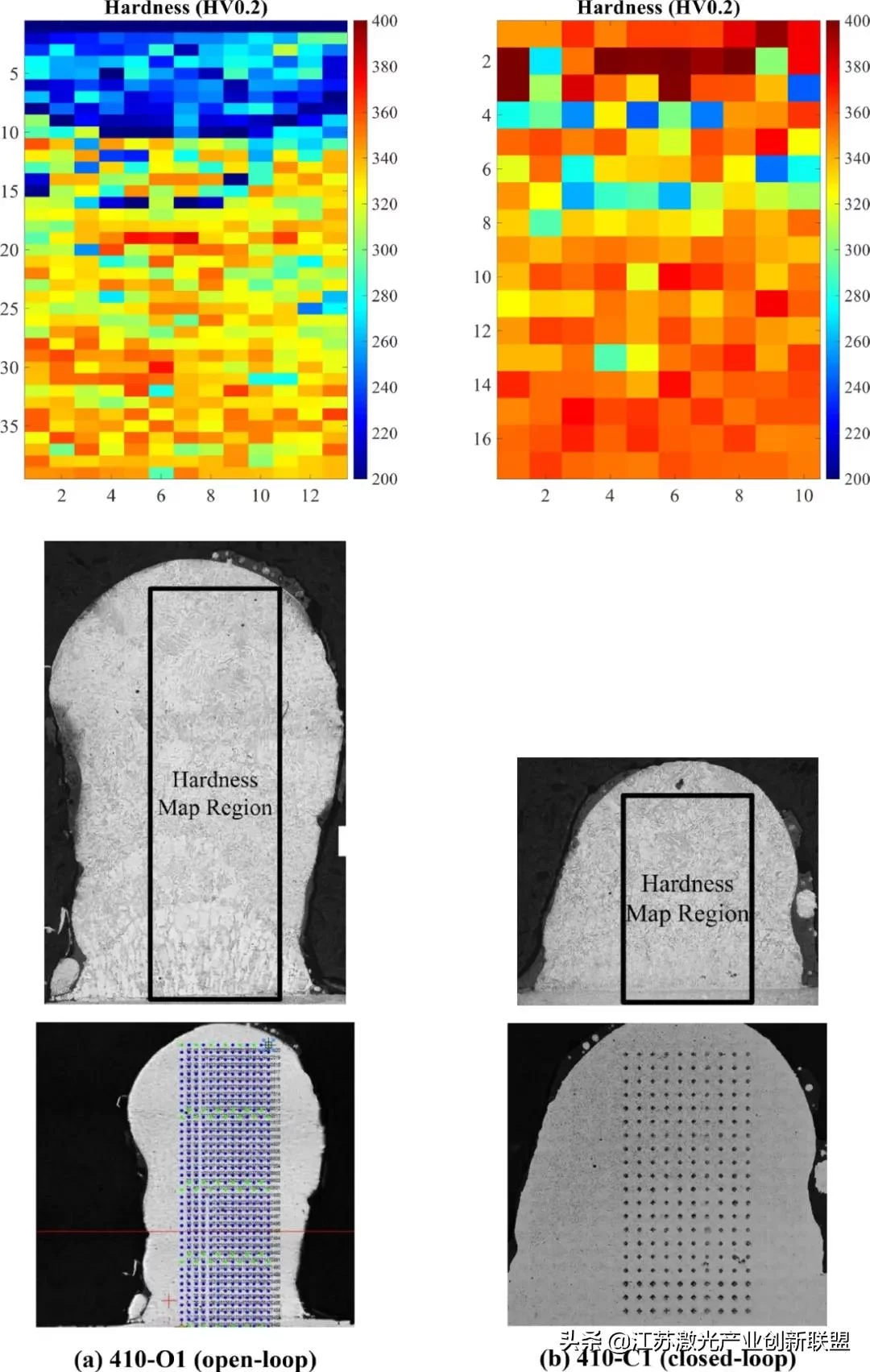
图15 开环和闭环奥氏体S410-LLAM沉积的硬度分布图。
如图10、图11、图12、图13所示,与微观结构结果直接相关的是,使用开环条件(图15a)产生的马氏体LAM沉积的硬度是不均匀的,而闭环样品具有一致、均匀的硬度分布(图15b)。比较表2中闭环和开环模型的硬度方差和标准偏差,很明显,闭环样品的硬度偏差比开环样品低得多。表2 计算的方差值加上相关的标准偏差压痕硬度剖面和测量图的开环和闭环镀层,如图15和16所示。
在图16中绘制并比较了不同加工条件下,如410-O2、410-O3、410-C2和410-C3的其他样品的开环和闭环沉积状态下,穿过LAM沉积马氏体不锈钢壁厚度截面的线硬度测量曲线。此外,这些测线测量的方差和标准偏差值计算并在表2中表示。在开环和闭环马氏体沉积中,每一层的硬度随着激光移动速度和冷却速度的增加而不断增加。
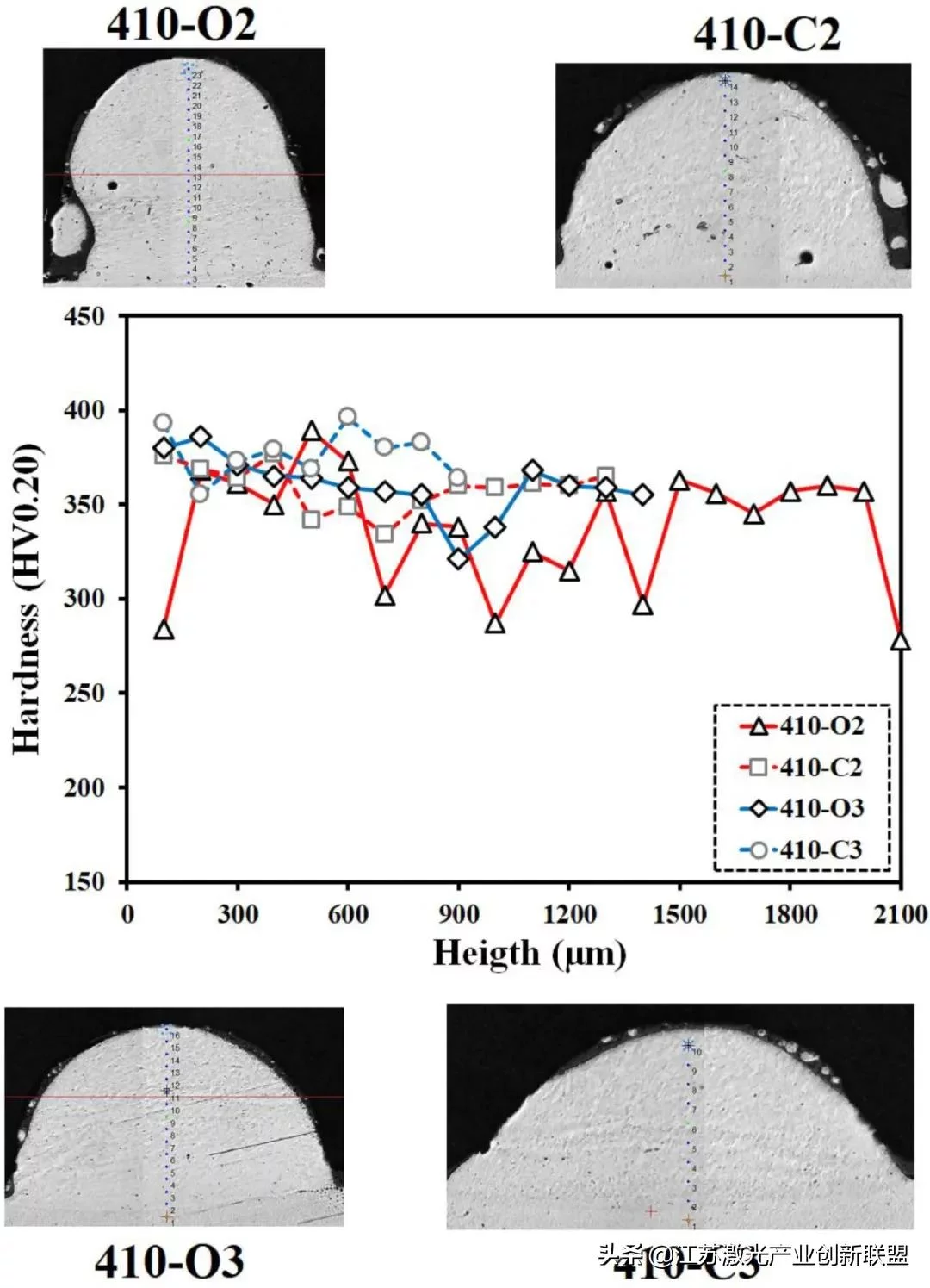
图16 在开环和闭环条件下,沿垂直方向激光增材制造的马氏体不锈钢结构厚度截面的硬度分布。
随着实时冷却速度的增加,马氏体板条和微孪晶尺寸的减小,使显微组织更加均匀,使显微硬度图谱更加均匀。在马氏体开环沉积中,硬度随沉积体从底部向顶部移动而降低。这主要是由于通过不同的冷却层,峰值温度不断升高,冷却速率不断降低所致。
在该合金中,在不发生马氏体相变的情况下,较低的冷却速率会导致层对层沉积过程中的晶粒粗化。例如,马氏体不锈钢的冷却速率较低,影响马氏体相变,促进粗马氏体板条和微孪晶。然而,对于采用闭环控制的沉积壁,保持恒定的冷却速率,可以得到均匀的微观结构特征,具有更均匀的显微硬度剖面(见图15和图16)。例如,开环样品410-O2(以恒定移动速度200 mm/min沉积)的硬度方差为930.31 (HV0.2)2,标准偏差为30.50 HV0.2。通过控制试样的冷却速率(所有层均控制在1100°C/s),硬度标准差降低到11.80 HV0.2,硬度变化减少了62%。因此,为了在DED沉积中获得一致的硬度曲线,需要实时控制冷却速率。
3.4. 展望
在本研究中,提出的马氏体不锈钢沉积闭环控制系统是提高激光增材制造对应件质量的关键技术。它可以被认为是一种很有前途的技术,用于监测和控制生物医学、航空航天和汽车等先进行业的功能性或统一产品。精确的制造方法提供了最小的稀释,集中的热源以及较低的热影响区域可使根据该闭环LAM策略生产的对应物在上述高科技应用中比传统的减法方法更具吸引力。与无任何反馈的开环沉积相比,根据普遍采用的实时或在线监测装置适用于高尺寸公差功能梯度结构中的局部微观结构控制。引入的闭环LAM程序的应用在降低晶粒结构细化导致的开裂敏感性以及随后仅通过监测沉积过程中的峰值温度和冷却速率来调整产品的完整性和机械性能方面具有很高的实用潜力。在本研究中采用了涉及共析奥氏体到铁素体相变的马氏体不锈钢沉积模型;然而,同样的方法也可用于未来其他梯度材料的微观结构控制。
4.结论
本研究开发了一种新型闭环激光增材制造(CLAM)系统,用于监测和控制LAM工艺中沉积材料的微观结构。CLAM系统利用热动机械监测和控制(TDMC)模块实时提取冷却速率、熔池温度和加热速率。该系统可以实时控制不同的工艺参数,以在整个沉积过程中将热动机械保持在所需的设定值。马氏体不锈钢用于研究闭环工艺的性能。冷却速率是激光金属沉积过程的主要有用参数,用于控制凝固过程中的外延生长和随后的固态马氏体相变。结果表明,在所有工艺条件下都发生了马氏体相变。
马氏体板条的尺寸在开环样品的不同层之间发生变化。另一方面,冷却速度的闭环控制使板条尺寸更加均匀。结果表明,在多层LAM产品中获得完全均匀的微观结构;除了初始凝固热动机械之外,还需要控制凝固后热动机械。根据实验结果,通过增加冷却速度,晶界或马氏体板条的尺寸不断减小,从而导致硬度不断增加。考虑到细小马氏体板条的形成,在LAM沉积后,通过将冷却速度提高1750°C/sec,马氏体不锈钢的硬度显著增加至~425HV。
作为主要结果,该开发的闭环LAM模型可适用于各种建筑行业,根据产生功能梯度和同质生成结构的不同策略,控制产品的微观结构和机械性能。然而,改进这项技术,同时监测熔池几何形状及其冷却速度,以达到先进产品的状态,仍然存在一些挑战。
来源:Closed-loopdeposition of martensitic stainless steel during laser additive manufacturingto control microstructure and mechanical properties,Optics andLasers in Engineering,doi.org/10.1016/j.optlaseng.2021.106680
参考文献:I. Gibson, D.W. Rosen, B. Stucker,Additivemanufacturing technologies: rapid prototyping to direct digitalmanufacturing(2010)
H. Fayazfar, M. Salarian, A. Rogalsky, D. Sarker, P. Russo, V. Paserin, etal.,A critical review of powder-based additive manufacturing of ferrousalloys: process parameters, microstructure and mechanical properties,MaterDes, 144 (2018), pp. 98 128, 10.1016/j.matdes.2018.02.018